driving autonomous with +150T of steel slabs

About
Company
Arcelor MittalLocation
Ghent, BelgiumCompetences
autonomous systems
computer vision
digital twin
robotics & machine control
model based design
sensor technology
reducing risks & errors
steel industry
driving innovation towards an autonomous slab carrier
relevance
At ArcelorMittal Ghent, innovation is always top of mind. To improve overall efficiency, the Belgian production site of the world-renowned steel group is looking to automate its ‘slab carriers’: enormous vehicles designed to handle steel slabs weighing 22 tons on average, for a total of 150 tons per transport.
vintecc’s experience with sensor technology, technical know-how and flexible service is proving to be a driving force behind the project.
“Throughout the project, vintecc has proven to be a knowledgeable and reliable partner. They are very open about the technological challenges, but also about the financial side of the project. When we started the project, we had no idea that there was so much automation expertise so close by. They are, without any doubt, an immensely valuable partner in this project.”

Leander Verhofstadt
Head of Departement - ArcelorMittal Ghent
challenge
“The site in Ghent has grown exponentially over the past 50 years,” explains Leander Verhofstadt, automation project leader at ArcelorMittal Ghent. To keep up with the increased productivity, we started an extensive modernization project to be unrolled in four phases:
- renewing and retrofitting the existing machinery
- restructuring the logistic models
- increasing worker safety,
- enhancing our automation capabilities.
Upgrading our slab carriers is a key element of that last phase.
Custom-made carriers
The slab carriers are specifically designed to carry steel slabs from the steel factory where they are produced to the hot-strip rolling mill. Leander: “This is very challenging process, and not just because of the weight. Slabs are stacked upon one another and can have different measurements, so the trick is to pick up the exact amount needed. The carriers we ordered for this project are custom made for our specific needs.”
Leander and his team want to turn the customized slab carriers into fully automated, self-driving vehicles that are able to navigate the site and pick up slabs. To make this possible, they called in the help of Vintecc.
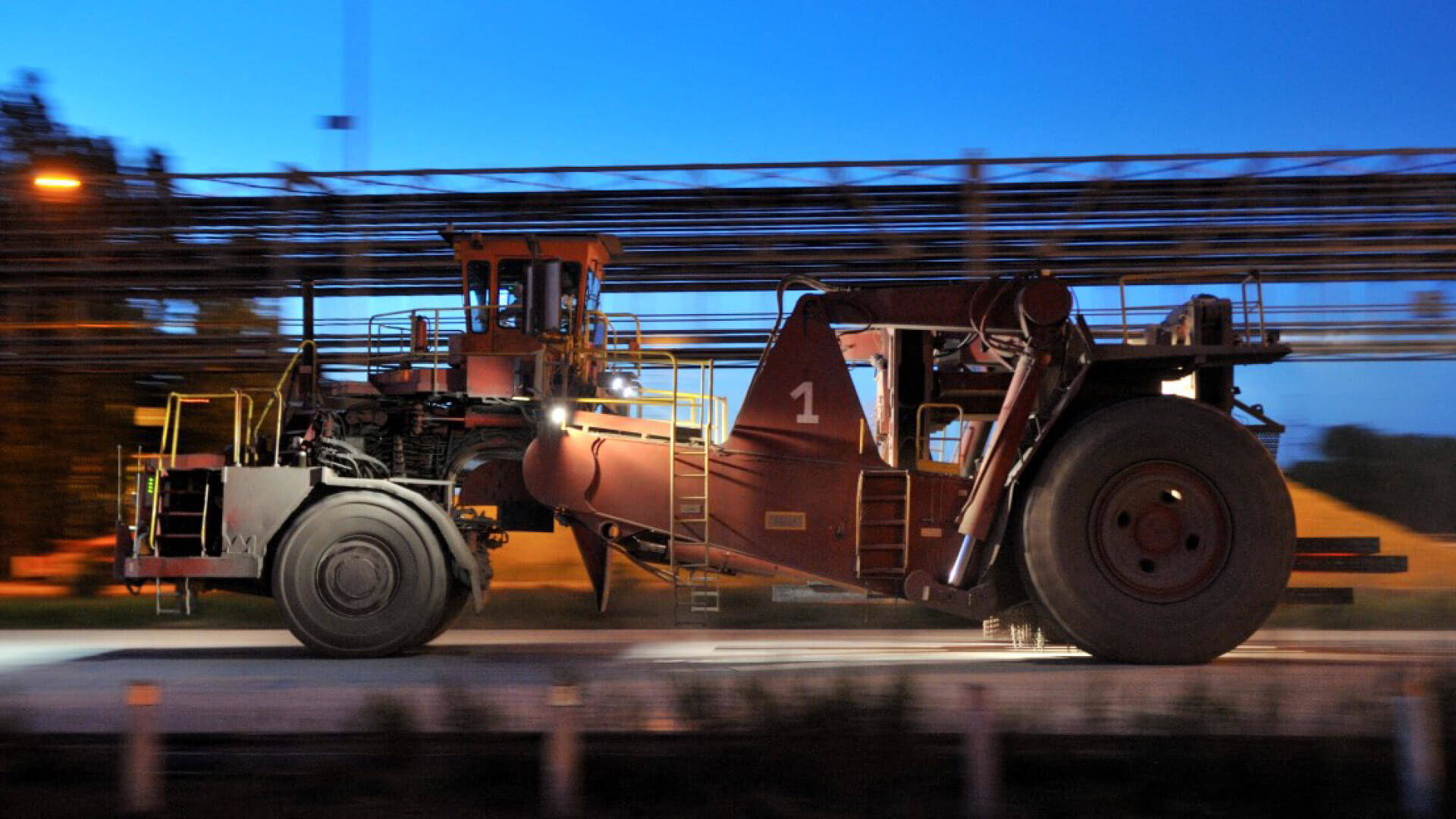
solutions
“As ArcelorMittal’s center of excellence, we have a lot of experience with automation,” explains Leander. “But automating vehicles is a very specific expertise, which requires a profound knowledge of sensor technology. In addition, we needed to have everything in place in terms of software and automation architecture before the first ordered carrier arrived.” In our search for the right partner, we came across a company called vintecc, which had experience in automating harvesting machines for Case New Holland.”
1 sensor study using digital twin
- A comprehensive sensor study was made to identify all the things the autonomous carriers need to recognize when navigating the site. During this study the amount of sensors and where to put these sensors was carried out as well.
- The study was sped-up using a digital twin of the slab carrier and the environment.
2 model based commisionning
- vintecc’s proven experience in model-based commissioning and the automation of harvesting machines quickly convinced Arcelor Mittal that vintecc had what it takes to successfully finalize the project.
- Candidate algorithms were implemented as components of a simulation controller model. The controller receives 3D data from the camera's and produces signals to control the movement of the slab carrier.
3 digital twin
- The environment was very challenging: it’s very hot, and the steel causes a lot of reflection. After developing a basic model, the team conducted closed-loop simulations of the behaviour on site of the slab carrier.
- The team fine-tuned the simulation model in the field to improve and optimize the control algorithm.
4 real life testing
- The next step was testing and finetuning the automation software. A jeep was equipped with the sensor configuration to drive around the site autonomously and to test the software.
results
1 successful first autonomous slab carrier
- A first slab carrier was successfully equipped with the soft- and hardware to drive autonomous around the slab field.
2 cruise control & navigation of an articulated vehicle
- The model that was generated from the virtual simulation in our digital twin worked from the first try. It performed exactly during field testing as we had expected.
3 fast iterations
- Fast iterations of the algorithm model were possible because new concepts or codes could be virtually simulated in any kind of circumstance. The team spent less time doing bug fixing.
4 full autonomous software stack
- The team developed a software stack which is robust and has proven its potential to deploy on all slab carriers of the ArcelorMittal Group.